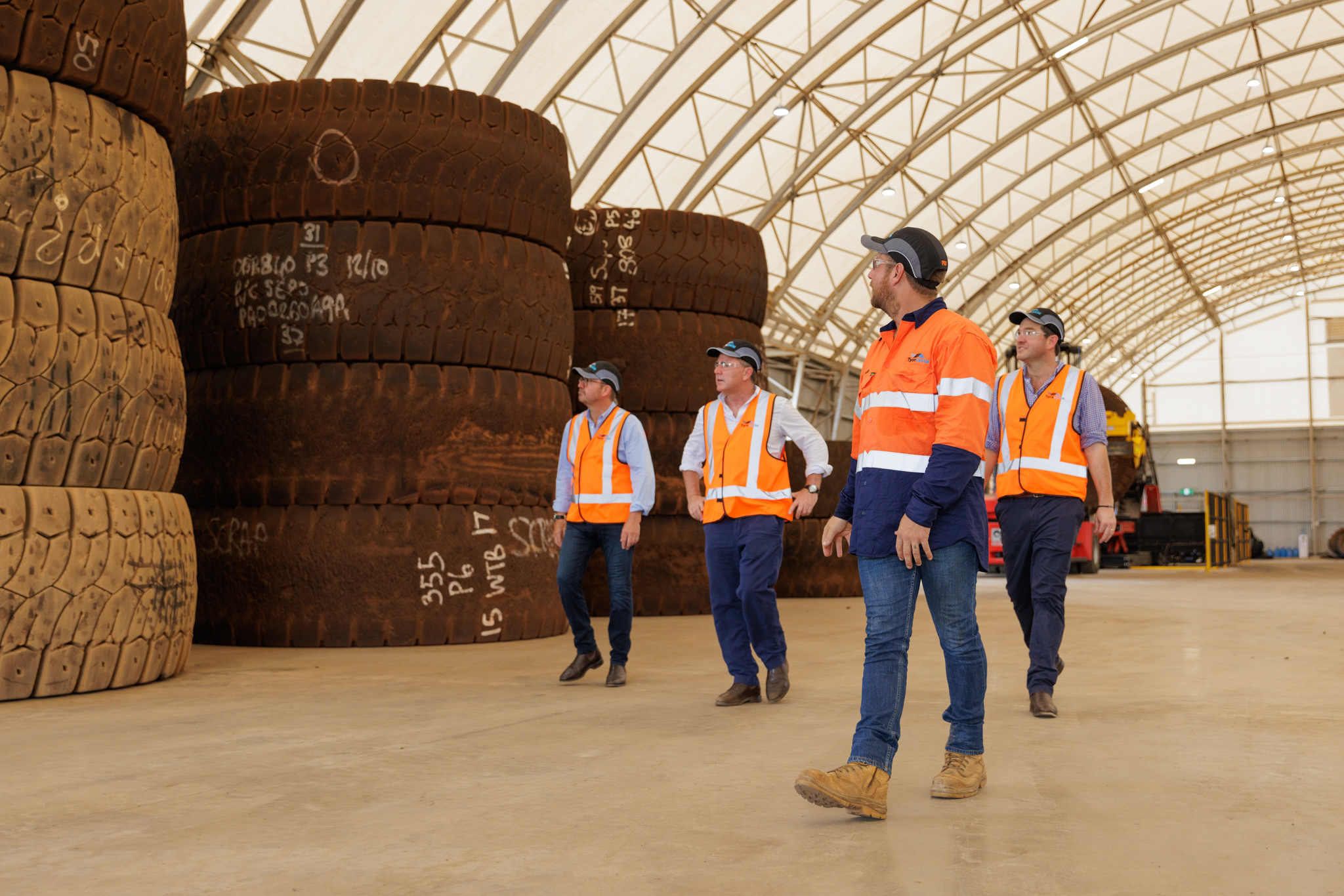
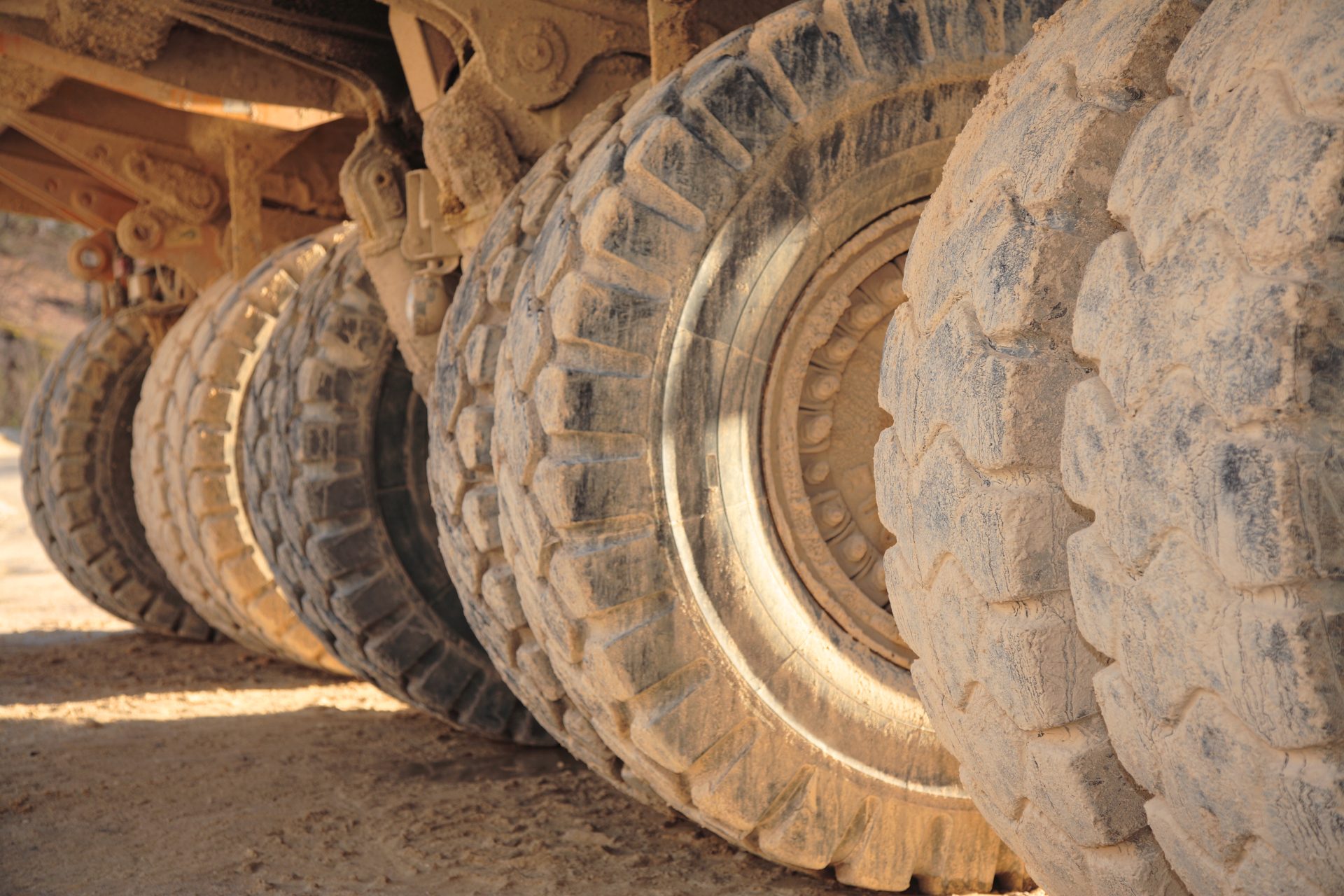
Tyrecycle’s OTR tyre recycling solution
Australia’s mining industry is a powerhouse, driving the economy with its vast operations. A significant part of mining activity is logistics, and the disposal of off-the-road (OTR) mining truck tyres has long posed a significant environmental challenge. Each year, 130,000 tonnes of OTR tyres reach their end of life in Australia, and fewer than 10% of these tyres are recycled, leaving significant ESG opportunities unleveraged for the sector. Enter Tyrecycle, a company at the forefront of transforming tyre waste management throughout Australia.
Leading the way in WA
Earlier this year, Tyrecycle unveiled its latest state-of-the-art tyre recycling facility in East Rockingham, near Perth. This facility has significantly grown Tyrecycle’s national tyre recycling capability and is a testament to the company’s commitment to sustainability. Importantly, this site will have a role to play in the recycling of Australia’s OTR tyres. Jim Fairweather, CEO of Tyrecycle, highlights the significance of this new infrastructure, “The East Rockingham facility is Australia’s largest and most flexible tyre recycling facility, both in terms of passenger and commercial tyres, but importantly OTR tyres too.”
Tyrecycle’s new East Rockingham site includes an OTR processing capability, but more significantly, it forms an integral part of the company’s grander plans to lead Australia’s OTR tyre recycling. Building on the success of the East Rockingham facility, Tyrecycle is now setting its sights on an even more ambitious project by developing Australia’s first dedicated OTR mining tyre recycling facility in Port Hedland. Scheduled to open by the end of the year, this facility will address the significant gap in OTR tyre recycling capability in Australia.
Fairweather highlights the opportunities associated with this endeavour: “Working with the mining industry, we’re seeing a dramatic change in willingness to recover and recycle OTR tyres. Mining companies recognise the importance of managing their waste streams responsibly, and we’re here to work alongside them to deliver more sustainable outcomes.”
Partnering with the mining industry
Tyrecycle’s initiatives are not just about building facilities; they are about working with the resources sector to lead a shift in the industry’s approach to waste management. The company’s collaboration with mining companies is pivotal in developing the right infrastructure needed to support more sustainable outcomes.
As Tyrecycle continues to expand its capabilities, the impact on Australia’s recycling landscape is profound. With the upcoming Port Hedland facility, Tyrecycle is set to revolutionise OTR tyre recycling, ensuring that these massive tyres are no longer a disposal challenge but a resource for new, sustainable products.
In the words of Fairweather, “Our goal is to deliver sustainable outcomes for our clients, where waste is a resource, not a problem. We are proud to already lead the way in tyre recycling across Australia. With our exciting new partnerships and infrastructure, we’re eager to lead the future of OTR tyre recycling as well.”
Tyrecycle’s new Port Hedland facility will have the capacity to process over 12,000 tonnes of OTR tyres annually, a capacity that is quickly gaining the attention of the industry. For this reason, the plant design is completely modular and has enough space to more than double the capacity on the Pt Hedland site. By integrating into existing logistics networks, Tyrecycle aims to provide an efficient mine-to-processing service, enhancing sustainability credentials for its partners. “Every tonne of crumb rubber used in asphalt mixes represents a greenhouse gas saving of 2,463kg CO2-e. Knowing your mining tyres took that path instead of being buried is a fantastic outcome for stakeholders and the environment alike,” Fairweather adds.